Managing all That Data
Product data management may have a bad rap, but making it a priority rather than an afterthought can help make the most of your design and machining information.
Product data management (PDM) is the use of software to manage product data created by other software. In its simplest form, it manages the storage and versioning of such data, and records who used or modified the data last. A good PDM solution will do this for all data types. For many companies, PDM is thought to be unobtainable, because they expect such systems to be cumbersome to use and implementation costs to be massive. The reality, however, is that every single manufacturing company needs a PDM system in order to be more profitable. Following is some background on how the outlook on PDM has become so negative.
The Data Timeline
Computer-aided design (CAD) technology was invented to streamline the engineering process, enabling engineers to work more quickly and to share their designs more easily. Soon after it was developed came its baby brother, known as computer-aided manufacturing (CAM). CAM software was developed to take the digital design data engineers came up with and turn it into manufacturing information that machines could understand. CAD and CAM revolutionized the world of engineering and manufacturing, however, this revolution also created a problem: data. Now that we had all of this digital data, we needed a way to manage it. Thus, the ugly stepchild was born: PDM. PDM products were developed about 6-10 years after the birth of the products for which they were written to manage. So PDM was an afterthought.
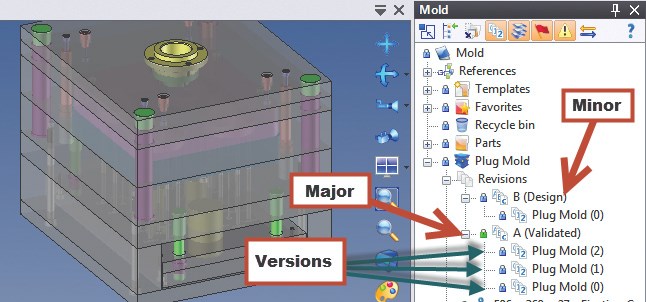
Integrated CAD/CAM/PDM tracks both major and minor mold base revisions.
This is why PDM solutions are considered too cumbersome and expensive to implement. If a PDM product has been developed that late in the game, the level of product integration will be skin-deep, at best, right? How can a product easily manage a solution after the fact like this? Well, it can be done, but at a cost. And that cost is usually in the form of an overly generic user interface that will need to be customized to specific customer needs with a lot of custom workflows to make the software work the way it was intended. The result is a hard-to-use, clunky solution.
A Managed Solution
But what if it didn’t have to be this way? What if the entire experience could be changed? What if, instead of making PDM an afterthought, you made it your primary thought, front and center in all your data-related operations? This means finding a software solution that manages all of the information that is created, used and deployed within your manufacturing processes and ensures that everyone involved in these processes works with the absolute latest version of the data. A solution like this would be integrated very tightly inside your CAD/CAM software, so users don’t even know they are using a managed solution.
Say you are a mold manufacturer that does everything internally, from the 3D design of the mold and the 2D detailed prints with the bill of materials to pulling electrodes and programming everything in between. You just finished completing a design, and your electrode specialists are pulling electrodes and beginning to program. At the same time, your mold base specialist is programming all of the base work, and the worker assigned to hard milling is programming your high-speed, five-axis mill for the cavity block. And this is a rush job, so you have virtually no time to think. Then the customer sends you a new database with a design change. How do you handle the design change and ensure that everyone gets the necessary updates without too much disruption to the operation?
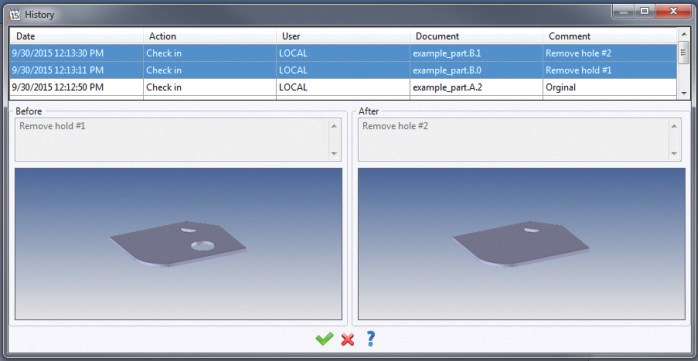
A managed PDM solution offers project backup, which enables users to compare original and revised mold/part designs.
You have two options. You can continue to manage this project yourself by checking every file to verify if an update is required, then head out to the shop floor to find each person involved in the project, alert them to the changes and inform them that all of their work will likely need to be redone. Or, you can work with a software solution that manages all of this for you: a PDM-based CAD/CAM solution.
In a PDM system, the design changes come through a managed solution. Engineering incorporates design changes, and when the design is approved, the engineers simply “close” the revision. This fires an automatic mechanism that notifies everyone downstream of the changes, instructing them to open their own files and hit “refresh.” In some cases, those downstream workers may need to fix or recreate portions of their work, but they will not have to start over again. Moreover, all the changes they and the engineers have made are protected by a previously managed revision. Oftentimes, this change in flow causes only a few minutes of disruption in the manufacturing process. Then everyone returns to doing what they should be doing — manufacturing.
A managed PDM solution like this also offers the benefit of project backup. Imagine a customer sends you a design revision. You make the required changes and then when you go to them for approval, you find they have changed their minds again. They want to go back to the original design. You hope you have a backup of the complete project, including the original design. With a managed solution, you are always protected with just such a backup. You can simply revert back to the previous revision, and all items downstream will return to that revision.
If PDM products are developed properly, with usability and cost effectiveness in mind, and then deployed appropriately, they are worth their weight in gold. Only then can these management solutions become attractive and attainable for the typical mold manufacturer.
Related Content
VIDEO: Perspective on A.I. and Mold Design
Bill Genc of TopSolid shares his perspective on the benefits of and barriers to using artificial intelligence in mold design.
Read MoreHow to Select a Mold Temperature Controller
White paper shares how cooling channel analysis, which collects maximum pressure drop, total flow rate and heat dissipation, eases the performance evaluation of mold temperature controllers.
Read MoreHow to Automate Process and Design
Moldmakers can improve their operations and stop wasting time by taking these six steps for process and design automation.
Read MoreTake Time to Save Time: 6 Steps in Mold Design to Reduce Back-End Troubleshooting
Westminster Tool shares how the one week it typically takes to perform these six steps in the design phase can save three weeks or more in an overall tool build.
Read MoreRead Next
Competition is Good
Losing business overseas motivated this moldmaker to re-engineer its tools, improve its processes and stand by its customer, ultimately winning the business back.
Read MoreMachine Monitoring Platform Improves Machine Utilization, On-Time Delivery
Using data from a machine monitoring platform, Westminster Tool added almost 75 hours of capacity per week by shortening warmups and starting CNC and EDM machines sooner.
Read More5 Steps to Get Started With Digitalization
Knowledge, a strong partner, an internal champion and an active regular participation in highly visible data will help smaller mold shops with digitalization.
Read More