Figure 1. Wire ties can act as a safety strap on small MUD inserts. Photo credit, all images: Injection Mold Consulting
While the function of a safety strap is to prevent a mold from accidentally coming apart during transportation and handling, its purpose is to protect people — not the mold or the machine.
The most common cause of mold halves separating is when a setup person uses only one eyebolt to lift a mold that doesn’t have a safety strap or a lifting bar. It doesn’t matter whether the eyebolt is in the ejection half or the injection half. When the hoist lifts the mold up, it is going to tilt in one direction or the other because an eyebolt hole is rarely at the mold’s exact center of gravity. Various factors, such as the clearance and lubrication between the leader pins and their bushings, and the angle and direction that the mold tilts, will determine whether half the mold will disengage and fall to the ground.
Another way a mold can come apart is when one side slaps up against a platen during setup. The conservation of energy and momentum can send the other side of the mold sailing toward the opposing platen, like the steel balls on the ends of Newton’s Cradle Pendulum. I’m sure many of you know some less common ways a mold can come apart, such as a racking system that’s difficult to maneuver, a mold cart with a wobbly wheel, an inferior wooden skid or an inexperienced forklift operator and a tight turn.
The best safety strap is one that also functions as a lifting bar.
The Importance of Safety Straps
Every mold should have a safety strap — especially small molds, such as MUD inserts. When personnel are handling a large mold, they do so with extreme caution, because they know if something goes wrong, it’s probably going to be, at the very least, loud. Small molds and MUD inserts are much less intimidating. They are often considered relatively harmless. This misconception is one reason people can get hurt.
Let’s say you have a small MUD insert for an 08/09 UF 321 frame, with a 1 7/8-inch laminated A-plate. The injection half of this particular MUD insert weighs about 32 pounds. If it ever disengages from the ejection half, say from a height of 34 inches — the standard height of several mold carts — it will hit the ground in 0.4 seconds. That’s less time than it takes to yell, “Look out!” and it is definitely less time than it takes to comprehend the situation and move safely out of the way. Due to gravitational acceleration, this 32-pound block of steel will hit the ground with a force of more than 90 foot-pounds. That’s more than enough to send a person to the hospital, and OSHA will probably want to know why.
The majority of the molds I have seen have their safety straps painted red. Despite this being the predominant color in our industry, it is not the correct color to use. OSHA has very specific color standards and they specify red for dangerous situations, “where an immediate hazard presents a threat of death or serious injury to employees.” The color yellow, which stands for caution, is more appropriate. It’s used, according to OSHA, for “minor hazard situations where a non-immediate or potential hazard or unsafe practice presents a lesser threat of employee injury.” However, employers are allowed to comply with the most current consensus standards applicable to their operations, rather than with the OSHA standard, when the employer’s action provides equal or greater employee protection.
In other words, red is acceptable. However, since employees must be trained as to the meaning of the various OSHA colors used throughout the workplace, these colors should be used consistently. Even though the purpose and use of a safety strap is not “out of the ordinary, unexpected or not readily apparent,” it is still important to train all relevant employees on the proper use of safety straps, the special precautions they should take and the potentially hazardous conditions associated with any misuse or abuse.
Safety straps should be located on the operator side of the mold. If they are located on any other side, there’s a good chance the setup man will not see them and attempt to open the mold while they are still engaged. Keep in mind that what the mold designer thinks is the operator side, and what the actual orientation of the mold is out on the production floor, may be two different things. In a case such as this, it is a good idea to put a placard on the other side of the mold, saying something to the effect of, “Remove safety strap.”
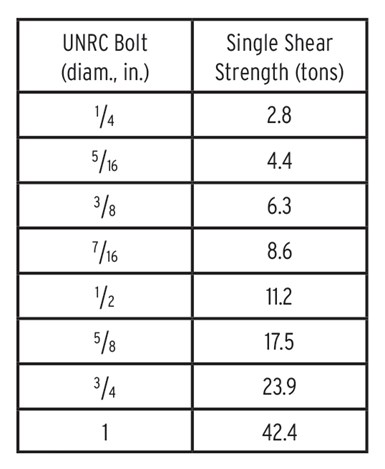
Figure 2. Single shear strength of ASTM A574 alloy-steel bolts.
How many of you have mold safety straps scattered around your shop, or perhaps an assortment stacked in a lost-and-found box? One way to control the number of straps that have lost their homes is to paint, stamp or engrave its corresponding mold number on the outer face. Ideally, you should use a mold strap design that does not require removing it from the mold at all — but there are not many of those commercially available to choose from. Whatever strap design you choose, if it’s face mounted on the side of the mold, you are most likely going to get dents in your tiebars. If a mold barely fits between the tiebars, you must remove the strap in order to hang it in the machine. That defeats the purpose of the strap and can be a definite safety concern. For these reasons, safety straps should be installed in a pocket — flush mounted with the operator of the mold.
On occasion, a mold may have multiple safety straps — one or more on either side. You see this from time to time on large molds, or molds that have spring-loaded plates, which cause the mold to be partially open when sitting on the bench. Some companies’ mold design guidelines specify installing straps on opposing sides of the mold. As long as you use an appropriately sized strap and mounting bolts, there is no need to use more than one, regardless of how large the mold is, or whether it has spring-loaded plates. In fact, multiple safety straps can be detrimental during the setup procedure, especially when they are out of sight. Once again, there is an exception to every rule. If the mold has multiple parting lines, such as three-plate, stripper plate or molds with a floating core plate, either a long safety strap, or multiple short straps are required — but all of them mounted on the operator side.
Choosing the Right Safety Strap
There are many different types of mold safety straps readily available from molding supply companies. Some are made from plastic, typically recycled glass-filled nylon. Others are made of steel. In my opinion, the existing plastic mold straps are too weak and have some inherent design flaws. They are supposed to be strong enough to keep the mold halves together, but weak enough to break if someone opens the mold in the press without removing them first. That sounds all well and good, but these nylon straps have multiple, glass-oriented knit lines in critical locations.
There’s also a strong likelihood that these exposed plastic straps will get damaged over time in a production environment. They are available in two different lengths but are not available in different amounts of holding power. The basic premise of a plastic safety strap makes a lot of sense; it’s the design and engineering of those currently available that I have a problem with. Since there is an exception to every rule, plastic wire ties as seen in Figure 1, wrapped around water fittings on both the injection and ejection halves of a small MUD insert, work very well at protecting personnel.
The metallic types of safety straps come in a wide variety of designs and construction. Some are cast iron, while others are machined carbon steel. Some look like dog bones. Others rotate or swivel. One unique design automatically unlocks when the mold is mounted in the machine, and locks back up when the mold is removed. Some of these straps incorporate shoulder bolts in their design, but most use standard alloy-steel socket-head cap screws (SHCS). Screws are used primarily in applications where they are in tension — fastening one object to another. In a safety strap application, they are subjected to shear, which is perpendicular to the fastener’s axis. The shear strength of a bolt is considerably less than its tensile strength.
If someone attempts to open a mold with a safety strap still engaged, every strap I have ever seen will break before any other damage occurs — and that’s a good thing. It protects the machine and the mold, without being a safety risk to personnel. One mold component supplier has the disclaimer, “To ensure adequate protection, use mold straps of sufficient size and quantity.” But how does the mold designer know what the sufficient size and quantity is?
Safety straps should be located on the operator side of the mold.
Ideally, a safety strap should be strong enough to prevent the mold from opening under various unforeseen circumstances, but always less than the holding power of the mold clamps and the machine’s mold opening force. The mold opening force varies widely depending on the type and size of the molding machine. It can range from about five tons to more than 100 tons. It is typically about 10% of the clamp tonnage, no matter whether it’s a hydraulic or electric machine.
Some safety straps have strength ratings of 2,000, 3,000 or 5,000 pounds. That is a static load rating. Dynamic loads are the bigger concern. Unfortunately, there is no way to accurately measure or predict how much dynamic load a mold will be subjected to under every circumstance. Assuming the strap is stronger than its mounting bolts, I would select the bolt size based on the mold opening force of the machine — with a large safety factor. For example, for a 100-ton machine with a 10-ton mold opening force, I might use 5/16-inch ASTM A574 alloy-steel bolts (not SAE-grade 8 bolts). From the accompanying table in Figure 2, a 5/16-inch bolt has a single shear strength rating of 4.4 tons. In this example, that is slightly less than half the mold opening force, and yet a very significant amount of holding force in the event of an accident.
In summation, a good safety strap and mold design will have the following features:
- One strap per parting line.
- Located on the operator side.
- Made of carbon steel.
- Appropriately sized ASTM A574 alloy-steel bolts.
- Painted, powder coated or otherwise decorated glossy OSHA yellow.
- CAUTION stamped or engraved in large, opaque black letters.
- Flush-mounted in a pocket.
- Never needs to be removed from the mold.
- Contains the corresponding mold number.
The safety strap shown in Figure 3 is one that I have developed over the years. It has all of the design features listed above. To disengage the strap: remove one screw, slide it over and reinstall the screw. To re-engage it: remove one screw, slide it over and reinstall the screw.
Despite all that I have said in this article, the best safety strap is one that also functions as a lifting bar. I discussed these types of bars in my May 2017 column, “Locating Rings, Platen Damage and the Center of Gravity.” These lifting bars have a large bolt fastened to each half of the mold to prevent separation, and an eyebolt hole at the mold’s center of gravity to keep it level when lifting. Even though the need to remove these large, robust lifting straps prior to opening the mold is glaringly obvious, they should still be painted OSHA yellow. If the setup man happens to forget to remove the lifting bar with its large bolts, there is a chance the mold clamps can rip right off the platen.
Updated and republished from Plastics Technology.
Related Content
Questions and Considerations Before Sending Your Mold Out for Service
Communication is essential for proper polishing, hot runner manifold cleaning, mold repair, laser engraving and laser welding services.
Read MorePrecision Welding Services Offer Rapid Turnaround Mold Repair and Reduced Molder Downtime
X-Cell Tool & Mold relies on outsourced, high-quality welding repairs from Lewis-Bawol Welding to ensure its customers' molds are back in production quickly and affordably.
Read MoreHands-on Workshop Teaches Mold Maintenance Process
Intensive workshop teaches the process of mold maintenance to help put an end to the firefighting culture of many toolrooms.
Read MoreWhat You Need to Know About Hot Runner Systems and How to Optimize Their Performance
How to make the most out of the hot runner design, function and performance.
Read MoreRead Next
What You Need to Know About Leader Pins and Bushings
There’s a lot more to these humble but essential mold components than you might suspect. Following the author’s tips could save much time, money and frustration.
Read MoreThink Safety: Eliminate Hazards Throughout the Shop
The tooling community is taking advantage of new products for safer mold shops and molding facilities.
Read MoreLocating Rings, Platen Damage, and the Center of Gravity: Part 3
Selecting the right locating ring and putting it to good use takes careful consideration.
Read More