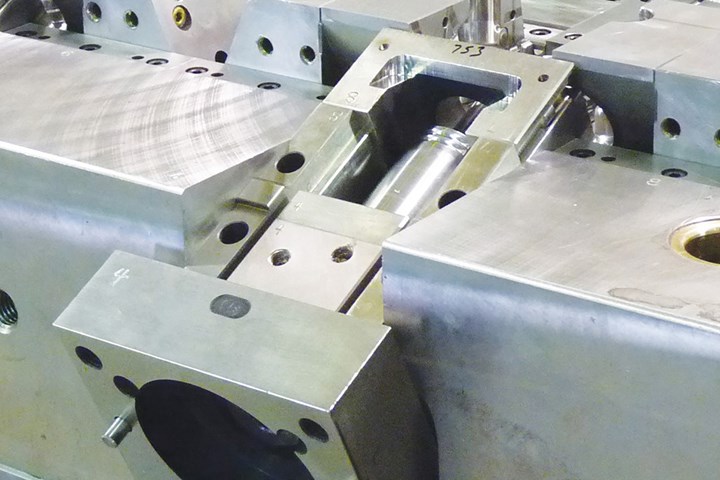
Achieving core preload means that you can make parts with perfect match lines, tighter tolerances and clean textures. Photo Credit: PFA Inc.
Molds in production often have various core pull side-actions, while designed with the best of intentions, do not fulfill current needs. Different materials, new molding parameters, requirements to drive glass below the surface or simply under-designing for the application, are just a few of the many reasons why mold performance suffers, often resulting in a core that may be flexing, moving or flashing.
Many molders have a list of problem molds. Because of this, the toolroom is challenged to keep them running and producing workable parts. While it could be argued that this is too much to ask without providing a solution beyond refitting and reworking the original design, a challenging mold also limits what can be done to improve the design without high costs or compromising the mold.
Many problems can be solved by simply providing enough preload force on the core to prevent movement. Nonetheless, blocks and pins only provide a backstop to a core and often provide little to no active support to prevent movement. These methods rely on steel’s mass or volume to minimize flex and movement to yield a “good enough” result. In this way, there is always some reaction to the forces of injection from the perfect positional geometry, rather than a proactive preloading of metal into position.
The Importance of Core Preload
Although many designers may not actively consider it, minimizing core movement via preload is often an essential part of a successful injection molding project requiring precision and uniformity. Preload is necessary to overcome injection forces, and choosing a core pull method that maintains preload at zero psi is often vital. Understanding what core preload is and its role in successful part production is the first step.
During the injection molding process, cores are placed under intense pressure and thermal variation that will often cause the core length to decrease or cause movement from the desired set position. These changes can often be seen on the completed part as if the entire core had “backed up” 0.010-0.020 inches or more. With core preload, these concerns are eliminated, and the molded part will retain the exact shape with no visible variations due to movement or flex. This is due to maintaining core preload force above injection force, even with no hydraulic pressure applied to the cylinder.
Simply put, achieving core preload means that you can make parts with perfect match lines, tighter tolerances and clean textures. Together, these unique characteristics create complex parts more easily, eliminating customer concerns, rework and scrap.
Although many designers may not actively consider it, minimizing core movement via preload is often an essential part of a successful injection molding project requiring precision and uniformity.
Preloading Side-Actions Solve Common Problems
What defines a quality side-action system is its ability to preload cores at incredibly high forces in a very small size. The Kor-lok hydraulic cylinder system, for example, achieves preload to the rated load and continues to maintain that preload even at zero psi hydraulic pressure. Once set using only a minimum of 1,500 psi, it provides 100% preload to rated load—approximately 10 times more force than a standard cylinder. To achieve zero movement, quality side actions should preload and maintain a force above injection pressure, and they should maintain that force without hydraulics.
A mold builder can solve many problems by retrofitting a mold with a more compact preloading and locking cylinder on existing molds. For example, let’s review the following common problems:
Problem 1: An underpowered hydraulic cylinder or overpowered heel block
The cylinder on the mold holds pressure on a small surface, or the heel block is insufficient to hold the core in position after the cylinder sets and heel block is engaged. The original design may have assumed the projected area was small and the seal would hold with minimal support. Regardless of the cause, the core is blowing back and flashing.
When considering a larger cylinder as a corrective action, there is not enough room on the mold, so the cylinder may not have enough force to hold the core. The problem may be hydraulic pressure drop to the cylinder during injection. For an overpowered heel block, there may be insufficient support structure available for modifications to eliminate movement.
A quality side-action system will provide high preload forces, allowing a much smaller cylinder to replace the existing cylinder and heel block. A blank mounting flange may be used to place the new mounting holes to match the current mounting locations. With the new side-action, the output force is large and locked in (similar to torque on a bolt), so the core will not move.
Problem 2: Parting line mounting
The cylinder mount on the mold is insufficient to hold the load from the core. Force on the core causes the mount to tip away from the mold. A heel block on the opposing side may reinforce the flange, but the gap allows flex and flash to occur.
A smaller-sized side-action system providing similar or greater force requirements may mount below the parting line and reinforce the core from that position. If a captured flange is needed for parting line mounting, the preloading capability allows preload even with the small gap at the flange to heel interface. Preload compensation adjusts for the flex of the mount, ensuring zero movement of the core.
Problem 3: Two movement cores
To allow the mold to fully close and then move the slide into place, a two-step set and block approach is commonly attempted. The first movement sets the core, and then a block or wedge is moved into position with a second cylinder. Often the load on the slide is too great for the second movement to support. Push back on the cylinder may side load the second function. As it is a two-step process, it requires two core pull circuits and additional cycle time to move two different slides.
The small and compact side-action serves both to move slides and to preload them to high forces. Frequently, a high-force side-action system may fit into a similar or smaller area as the original standard cylinder and provide both functions quickly and easily. The combination of both set and preload/lock makes the new process only a single action, improving setup and cycle speed.
Preload is necessary to overcome injection forces, and choosing a core pull method that maintains preload at zero psi is often vital.
Problem 4: Flashing cores on a carrier
Multiple cores on a single carrier plate may result in some of the cores lifting and flashing. The carrier is not stiff enough to minimize flex, so the outer cores away from the center of the applied force and the supporting structure often lift. Eliminating all flex is challenging as the plate resists load and is not preloaded.
While stiffening the plate should always be considered part of the corrective action, timing the outer cores to contact slightly before the inner cores and using a much larger force preloading side action to pre-flex the carrier slightly can produce the desired results. The approach can also be used on very long thin slides by placing a camber in the slide and then preloading it into place along a support stop.
Problem 5: Narrow operating window
Molds designed to initial injection parameters may not have the ability to tolerate unexpected changes in the production environment, potential part changes, mold modifications or pressure increases. A few examples of when a mold must operate outside the originally intended operating envelope include increasing pressure to push a harder material, driving glass under the part’s surface, improving the finish and moving knit lines. In these cases, additional pressure and movement yield out-of-spec parts and possible flash.
Due to the combination of high force and small size, preloading side-actions may provide a reasonable amount of overcapacity when initially designed into the application. In these cases, a slight overdesign in performance greatly widens the operating window at little cost. Retrofitting with a preloading side-action can often be done easily as a replacement to a standard cylinder or by mounting external to the mold base and reaching inward to preload the slide. This minimally invasive approach can eliminate complex rework and improves performance by greatly expanding the operating window.
Related Content
Forces and Calculations Are Key to Sizing Core Pull Hydraulic Cylinders
To select the correct cylinder, consider both set and pull stroke positions and then calculate forces.
Read MoreSolving Mold Alignment Problems with the Right Alignment Lock
Correct alignment lock selection can reduce maintenance costs and molding downtime, as well as increase part quality over the mold’s entire life.
Read MoreAdvantages and Disadvantages of Copper and Graphite Electrodes
Both copper and graphite provide approximately the same end result, so it is important for a shop to consider the advantages and disadvantages of each material in order to discover what would work best in their shop floor environment.
Read MoreLaser Welding Versus Micro Welding
The latest battle in finely detailed restoration/repair of mold materials.
Read MoreRead Next
Mold Side-Actions: How, Why and When They Work
Understanding the effects of injection on the core, slide and associated components is critical to selecting the best side-action methods for a given application. This first of two articles will discuss the basic physics underlying all side-actions.
Read MoreMold Side-Actions: Applications Rule the Action
With a firm understanding of the effects of injection on the core, slide and associated components, this second of two articles will discuss emerging modular technologies which provide alternatives to the limited solutions previously available.
Read MoreForces and Calculations Are Key to Sizing Core Pull Hydraulic Cylinders
To select the correct cylinder, consider both set and pull stroke positions and then calculate forces.
Read More