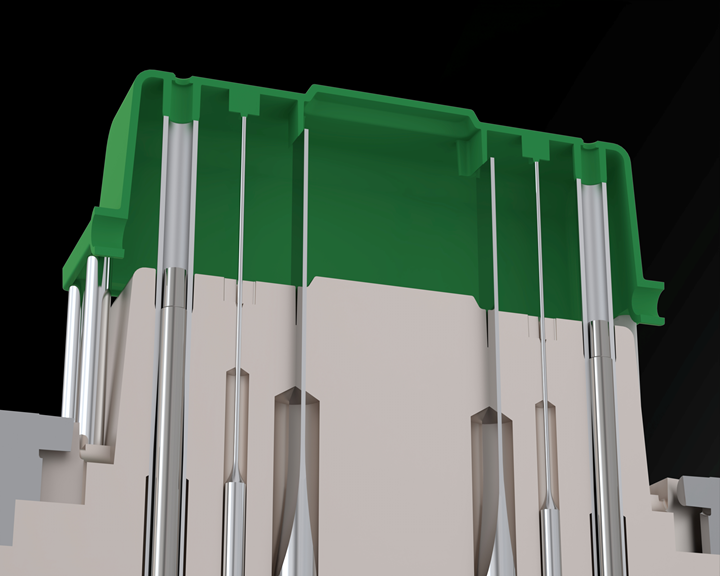
Pins, blades and sleeves, shown here under a part with ribs and bosses, ensure proper ejection of the part while also enabling venting. Photo Credit, all images: PCS Company
The most frequently used component of a mold’s ejection system is the ejector pin, which includes variations such as sleeves and blades. Part size, draft angle, shape complexity, vertical wall height and the type of plastic being molded all contribute to determining the appropriate pin type, location and quantity. Due to extensive use, ejector pins are sometimes considered a commodity item — something that is indistinguishable between suppliers of the same types of pins. However, ejector pins are not truly commodity items because there is no “one pin type fits all” solution.
To help guide your selection process among the various types available, this article reviews the materials, treatments and coatings used to produce ejector pins and best practices for using them.
Ejector Pin Basics
To perform optimally, ejector pins must possess certain fundamental characteristics, including a high degree of strength, toughness and wear resistance, and the ability to retain edges. More application-specific characteristics include hot hardness, which is the material’s ability to retain hardness at elevated temperatures, and varying degrees of corrosion resistance and lubricity, depending upon the type of molding application.
Geometric accuracy is another fundamental requirement for a pin’s performance and life. Ejector pins must be manufactured to tight tolerances and specifications. Roundness, straightness and high-quality surface finishes are all critical to function or premature flashing and galling, for example, may result.
It’s the combination of material, treatments and coating that make a pin suitable for a given application. However, enhancing one or more of these characteristics may require compromising the effectiveness of others. Leading ejector pin manufacturers work continuously to find the best combination of characteristics that will provide higher pin performance in answer to customers’ needs.
It’s the combination of material, treatments and coating that make a pin suitable for a given application. However, enhancing one or more of these characteristics may require compromising the effectiveness of others.
Material Benefits
Becoming familiar with the materials used for manufacturing ejector pins and their properties will help mold designers and moldmakers make better choices. Here are some of the most used materials and their qualities.
- H13: A chromium-molybdenum hot work tool steel offering an excellent combination of strength and toughness. Its hot hardness and thermal shock resistance values are the highest among the various materials used. Hardness values can reach 54 HRC, which is slightly lower than some other through-hardened steels. However, the lack of wear and corrosion resistance is overcome by the addition of surface treatments. Due to its unique combination of required properties, this is probably one of the most widely used materials for ejector pins globally.
- Through-hardened, cold-work: Ejector pins, blades and sleeves are also manufactured from O1, A2 and some other high-carbon cold-work tool steels. They are through-hardened to around 60 HRC, offering good wear resistance and making them suitable for molding commodity plastics and various materials that do not require high mold temperatures.
- Through-hardened, high-temperature: Belonging to the high-speed steel (HSS) category, M2 steel offers excellent strength with medium toughness. Like H13, it has high hot hardness and thermal shock resistance. M2 steel is through-hardened and can achieve up to 64 HRC, giving it excellent wear resistance. Another quality is its ability to retain sharp edges.
- Stainless steel: When molding extremely corrosive materials, stainless steel ejector pins are a viable option. Through-hardened, their values can reach between 50 and 60 HRC, depending on the grade. To achieve high hardness and wear resistance, martensitic grades are typically used, and it should be noted that they are not ranked the highest within the stainless steel family for their corrosion resistance. However, they are better suited for use as ejector pins due to their combined qualities of strength, toughness and hardness.
- Copper alloys: Copper alloys are primarily used for making core pins. Under some extreme conditions, when fast heat transfer becomes a priority, they are used for making ejector pins, too. Both beryllium-copper and beryllium-free grades (for medical use) may be available. Copper alloy material has its limitations due to its softness and lower strength.
Mold designers have an array of options for ejecting parts, including (shown left to right) through-hardened H13 nitrided pins, through-hardened H13 step pins, H13 nitrided ejector sleeves, A2 through-hardened, thin-wall ejector sleeves with an electroless nickel coating, through-hardened ejector blades, M2 steel through-hardened ejector pins, through-hardened H13 ejector pin with a chrome surface treatment and through-hardened H13 ejector pins with black nitriding.
Ejector Pin Choices
Understanding ejector pin characteristics and material types provides a good foundation for what to use in a mold. Still, there is more to know or to be confused by, given the many options suppliers offer today. Here is a collection of commonly available ejector pin products with noted composition and advantages.
- H13 through-hardened and nitrided pins: These pins are typically available with core hardness in the range of 48-55 HRC and surface hardness of 65-74 HRC. Ion nitriding is one of the commonly known surface treatments. This pin type is universal and used for both high- and low-temperature applications. It has a high operating temperature, close to 1112° F [600°C], making it suitable for use in metal injection molding (MIM) and die-casting dies as well. It should be noted that when machining pins that are nitrided, be careful to avoid microchipping. Grinding and EDM are the preferred processes.
- Through-hardened, cold-work steel pins: Offering good wear resistance, this steel pin type is available mostly in metric sizes. They are ideal for applications with low-to-medium mold temperatures. The pins with no additional coating or treatment are an economical option, offering good performance and life. Remember that pins made from these steels start to anneal or soften with exposure to high temperatures.
- High-hard M2 steel pins: These versatile pins are typically offered with no additional coating or treatment, yet they are a high-performing and durable option for molding resins of all types. The high hot hardness of steel enables use in cold as well as hot applications. Their ability to retain sharp edges ensures prolonged, flash-free molding in high-precision molds such as those for connectors. Due to the pins’ high strength, smaller diameters or sizes are possible, making themt suitable for molding miniature parts. Equally hard from the core to the surface, these pins do double duty as core pins in combination with sleeve ejectors.
- Armor- or chrome-plated H13 pins: The application of chrome boosts the surface hardness of H13 pins to around 70 HRC. Applied very thinly yet dense in its composition, the coating/plating offers excellent wear resistance along with some improvement in corrosion resistance. The coefficient of friction is very low, at around 0.20 to 0.25, which makes the pin highly durable. All of these qualities make the plated H13 pins a good option for high-production molds and cleanroom environments. Note that the coating may have a lower operating temperature than the core H13 material. For example, one such pin type has an approximate operating temperature of 842°F [450°C]. Also, the coating may not be appropriate for molding PVC. As plating processes may vary among suppliers, it is best to check these factors for suitability.
- Black nitride H13 pins: A newer offering, black nitride H13 pins
- DLC-coated pins: Diamond-like carbon (DLC)-coated pins are ideal candidates for cleanroom and medical applications as they can be run without lubrication. Usually made from cold-work steel, they are through-hardened to around 60 HRC. The coating offers excellent wear resistance and is anti-adhesive, with a very low coefficient of friction of 0.1 to 0.15. Operating temperatures can be as high as 662°F [350°C]. Also, DLC pins have a surface hardness of around 3,000 HV, which far exceeds any other pin type discussed in this article. All of these qualities make this pin a high performer, offering excellent durability.
- Stainless steel pins: These are an optimum choice for molding highly corrosive materials such as PVC. They are also well suited to medical and other cleanroom applications. Grade selection varies among suppliers, so evaluate other properties to help choose the right one for the application at hand. If used in high-temperature applications, check with the manufacturer regarding suitability because both corrosion resistance and hardness can be reduced at elevated temperatures.
Proper design of the mold’s ejection system is crucial to its production, life and performance, including its molding speed and smooth, interruption-free operation. This information serves as a trustworthy guide for making the right ejector pin choices.
Related Content
6 Ways to Optimize High-Feed Milling
High-feed milling can significantly outweigh potential reliability challenges. Consider these six strategies in order to make high-feed milling successful for your business.
Read MoreForces and Calculations Are Key to Sizing Core Pull Hydraulic Cylinders
To select the correct cylinder, consider both set and pull stroke positions and then calculate forces.
Read MoreMaintaining a Wire EDM Machine
To achieve the ultimate capability and level of productivity from your wire EDM on a consistent, repeatable and reliable basis, regular maintenance is a required task.
Read MoreIt Starts With the Part: A Plastic Part Checklist Ensures Good Mold Design
All successful mold build projects start with examining the part to be molded to ensure it is moldable and will meet the customers' production objectives.
Read MoreRead Next
Solving Mold Alignment Problems with the Right Alignment Lock
Correct alignment lock selection can reduce maintenance costs and molding downtime, as well as increase part quality over the mold’s entire life.
Read More5 Hot Runner Tips for Moldmakers and Molders
Best practices for initial hot runner tryouts and effective preventive maintenance.
Read MoreHow to Build a Better-Performing Hot Runner Mold
Early stage communication across the supply chain about design considerations optimizes hot runner mold performance.
Read More