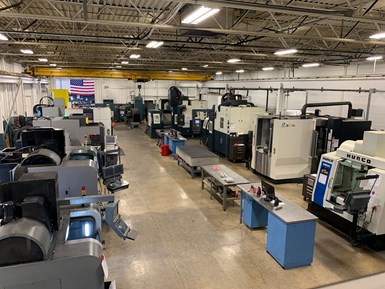
TK Mold & Engineering operates with a team of 25, plus seven CNC machines, multiple lathes and drills, and a five-axis sinker EDM from two facilities totaling 25,800 square feet/2,397 square meters of space in Romeo, Michigan. Photo Credit: TK Mold & Engineering
Romeo, Michigan-based TK Mold & Engineering Inc. was founded in 2003 by Tom and Krista Barr, who purchased assets and a building that had previously housed another moldmaker. Tom, who describes himself as a third-generation moldmaker, is president of TK Mold, and Krista, who is also a licensed master social worker (LMSW), is director of employee development.
“Team culture is very important to both Tom and me,” explains Krista, who says they actively work to create an environment where all employees have a voice and feel valued. “We hire quality people, do quality work and provide a quality experience. We operate our shop with an ‘all hands on deck’ philosophy. Most of our shop personnel are cross-trained in multiple disciplines and can execute multiple tasks.”
With a team of 25, seven CNC machines, multiple lathes and drills, and a five-axis sinker EDM housed in two facilities totaling 25,800 square feet/2,397 square meters of space, TK Mold designs tools and parts and builds up to six tools/month. The company also makes engineering changes and offers maintenance and repairs on anyone’s tools. Last year, TK Mold added low-volume custom injection molding (up to 50,000 pieces/year) to ongoing mold sampling services using three presses of 200, 300 and 730 U.S. tons/181, 272 and 622 metric tons. Most mold customers hail from the automotive and consumer goods markets, but the company also makes tooling for the aerospace and medical segments. Most molded products are for consumer goods customers.
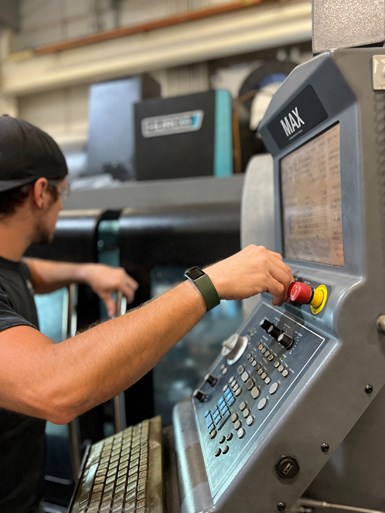
The company builds molds for customers in the automotive, consumer goods, aerospace,= and medical segments and also injection molds products for consumer goods. TK Mold is ITAR registered and ISO 9001:2015 certified. It was named the AMBA Mold Maker of the Year in 2022 and Trail Blazer of the Year in 2023. Photo Credit: TK Mold & Engineering
Over the last two decades, 80% of the company’s tooling has been produced in steel and the balance in aluminum. During that period, 80% of the tools were for injection molding (straight injection, two-shot, rotary and pick and place) ranging from one to eight cavities and frequently with side action. The remaining 20% of production tooling was for compression molding. Injection tooling is typically sized for presses ranging from 85 to 730 U.S. tons/77 to 662 metric tons, with the company’s sweet spot falling between 200 and 500 U.S. tons/181 and 454 metric tons. Many of these tools are designed for precision molding to hold tolerances of ±0.050 millimeter/0.002 inch on the AZ axis of a plastic fitting.
Given its customer base, TK Mold is ITAR registered and ISO 9001:2015 certified. It was named the AMBA Mold Maker of the Year in 2022 and Trail Blazer of the Year in 2023. Very active in mentoring young people in toolmaking, the company has a Registered Apprenticeship Program with the U.S. Department of Labor; was named Macomb Career Technical Education Administrator’s Association Outstanding Business Partner for 2018-2019; and Romeo High School Business Partner annually from 2019 through 2022. TK Mold also received the Macomb County Outstanding Business Award in 2021 and Special Congressional Recognition and Special Senatorial Recognition certificates in 2019.
Benefits of Integrated CAD/CAM
Since its inception, TK Mold has used integrated Cimatron CAD/CAM software to streamline its workflow from quoting and design straight through to machining and EDM to assembly. The company currently has 10 licenses: three Cimatron Designer Solution (CAD), five Cimatron NC Solution (CAM), one EDM Solution (electrode design and manufacturing) and two floating View Only licenses for personnel operating CNC and EDM machines.
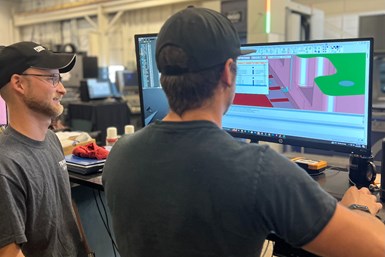
Since its inception, TK Mold has used integrated Cimatron CAD/CAM software to streamline its workflow from quoting and design straight through to machining and EDM to assembly. The company also periodically invests in advanced training to ensure its entire team is using the robust software to its fullest. This has paid off by shortening tool delivery lead times and increasing shop productivity. Photo Credit: TK Mold & Engineering
“Years ago, we had one guy using a different package, but we switched exclusively to Cimatron as we found that managing data was much easier when everyone used the same software, especially for updates,” notes Tom. “This way, we never have translation issues when moving data between packages. Also, because it was designed for the tool and die industry, Cimatron is very user-friendly for moldmakers.”
“The ability to take a part and start making parting lines with Cimatron’s QuickSplit feature allows us to streamline designs from the time we kick off a job,” adds Jonathan Salter, TK Mold CNC manager. “Cimatron offers many libraries from all the major vendors that allow you to design anything from gates to runners to ejector pins with just a few clicks of the mouse. The tools they’ve incorporated in their software really help with all aspects of design — from slides and lifters to waterlines and mold bases — and shorten the amount of time it takes to move from design to production to completion.”
“What sets us apart from our competitors is that from the very beginning, our software was developed to address the needs of the tool and die industry.”
Designed for Tool and Die
Cimatron pioneered many features that make mold design much faster, such as QuickSplit (top left), splitting of cores/cavities and slides/lifters to quickly detect potential problems; Quick Compare (bottom left), mathematical comparison of new and old part data as multiple team members in different departments work on a tool; and Quick Electrode (middle right), automatic electrode design and toolpath generation as tool geometry is set. Photo Credit: Cimatron
Cimatron began life in 1982 as an Israeli software company named Microcad that focused on developing manufacturing software for the country’s Air Force. Within 2 years, the company introduced its first CAD and CAM packages designed for medium-sized tool shops. In 1990, the company changed its name to Cimatron Ltd. and introduced its first integrated CAD/CAM package called Cimatron IT. In 2008, Cimatron merged with CNC machining software provider Gibbs and Assoc. and added GibbsCAM to its product offering. The joint company collaborated with LEDAS (now LGS 3D) in 2010 to add motion simulation and crash detection capabilities, which were subsequently licensed and integrated into the package. By 2013, Cimatron was researching additive manufacturing and developing tools to incorporate conformal cooling into mold designs. In 2015, Cimatron was acquired by 3D Systems, which sold the company in 2020 to Battery Ventures, which, in turn, added SigmaNEST software to the product portfolio before an acquisition by Sandvik in 2021.
“What sets us apart from our competitors is that from the very beginning, our software was developed to address the needs of the tool and die industry,” explains Ralph Picklo, Cimatron Americas sales director. “If you’re designing molds, dies, fixtures or gages, why wouldn’t you use integrated, efficient, user-friendly software dedicated to designing and producing the very things you’re building every day?”
He adds that most major software packages used in the plastics industry offer CAD or CAE or process simulation but aren’t integrated with CAM, and the handful that do offer CAD/CAE/CAM still don’t have specific tools to design and manufacture molds efficiently. With Cimatron, the entire mold design and production functions are fully integrated, yet the system still offers the flexibility to make last-minute changes. That’s why the software can help shops reduce tool delivery times by up to 70% and ROI for the software is typically achieved within 6 months.
“Thanks to our digital connectivity, templating, a standard mold component catalog and direct integration with the CoroPlus Tool Library and TDM tool management system, as well as automation of repetitive processes, Cimatron makes the design process more efficient from the very start,” Picklo continues. “In fact, it enables a designer to specify a company’s standards and then apply them to every job so they don’t have to reinvent the wheel each time.” He says that as tool delivery times keep getting shorter, companies need software that’s dedicated and streamlined for their industry. “Our software allows multiple users in different departments to work on the same job at the same time, drastically shortening tool delivery times while ensuring all users work with the most current data while tracking all of the engineering changes.” Once the tool is designed, CAM files are produced and then converted to G-code to rough and finish mill in two-, three- and five-axis CNC machines. Additionally, the software generates files to burn electrodes on sinker EDMs without manual input.
A good example of how Cimatron automates and speeds the design process is an automotive mold TK Mold’s team recently completed. “Upon kicking off a job, many of our customers give us a range of different press sizes a mold may go into, which allows us to change mold base sizes to find the one that best fits our customer’s needs,” explains Salter. “Cimatron enables us to easily apply mold bases in our design directly from a drop-down menu, rather than requiring us to go to the websites of mold base suppliers and download a CAE model for each mold base we think we might need and then manually load it into our CAD package. Features like that really simplified things on this challenging job with a short lead time and many engineering changes. We were able to switch between mold bases of different sizes without having to input more information from external sites.”
Because Cimatron is a fully integrated CAD/CAM package specifically designed for the tool and die industry, it helps designers and machine operators design machine features like multiple pockets in multiple heights (top left), five-axis tilt for milling (bottom left) and automatic or custom conformal cooling channels in additively manufactured inserts (right). Photo Credit: Cimatron
Staying Ahead of the Game With Advanced Training
Despite using Cimatron for two decades, TK Mold periodically takes the time and invests in having the supplier come in to conduct advanced training, especially as new features are added to the software.
“While you can start using it right away, given how robust Cimatron is, it does take time to master the software,” adds Tom. “To maximize our effectiveness and keep shortening our tool delivery lead times, we make it a practice to bring Cimatron in to conduct advanced training for our team and this investment really pays off by allowing us to use the software more efficiently with each major upgrade. The best part of this extra training is that it allows us to ask questions about our processes and tools we’re currently working on.”
“Tom and Krista always want to take advantage of the latest technology, so they’re willing to invest in advanced training sessions that move their team from average users to pro users, which really streamlines their process and makes their shop more profitable,” says Picklo, who adds that this should be a lesson to all companies who want to avoid getting stuck in a rut. “I have customers who’ve told me that if they can knock 1 minute per day off the time it takes each of their 16 designers to accomplish a task, then that multiplier really adds up to significant time savings at the end of the month. Some shops say they can’t take the time to do the extra training, but I say to them, they can’t afford not to take the time.”
Related Content
Five-Axis Vertical Mill Increases Mold Shop Capacity by Reducing Setups
Zero Tolerance now processes blocks — from squaring to waterline drilling to rough and finish milling — on a single five-axis CNC mill, reducing setups and moving blocks in/out of multiple machines without sacrificing accuracy and surface finish.
Read MoreCAM Automation Increases Mold Production, Quality
Mold builder switches CAM software package after 20 years to take advantage of innovative programming strategies that reduce mold machining programming and processing times.
Read MoreConsiderations for Mold Base Material Selection
Choosing the right material can greatly affect the profitability and cost of your application.
Read MoreOEE Monitoring System Addresses Root Cause of Machine Downtime
Unique sensor and patent-pending algorithm of the Amper machine analytics system measures current draw to quickly and inexpensively inform manufacturers which machines are down and why.
Read MoreRead Next
VIDEO: CAD/CAM with the Moldmaker in Mind
Ralph Picklo, Director of Sales for Cimatron at CAMBRIO, shares what it means when CAD/CAM is created with the mold builder in mind.
Read MoreMaking Mentoring Work | MMT Chat Part 2
Three of the TK Mold and Engineering team in Romeo, Michigan join me for Part 2 of this MMT Chat on mentorship by sharing how the AMBA’s Meet a Mentor Program works, lessons learned (and applied) and the way your shop can join this effort.
Read MoreICYMI: MMT Chats: True Leadership Leads to Mentoring, Part 1
This trio from TK Mold and Engineering in Romeo, Michigan, joins me to discuss the role of leadership and culture in mentorship. This episode is brought to you by ISCAR with New Ideas for Machining Intelligently.
Read More